Understanding Capabilities Up-Front Will Eliminate Public Warehousing Headaches
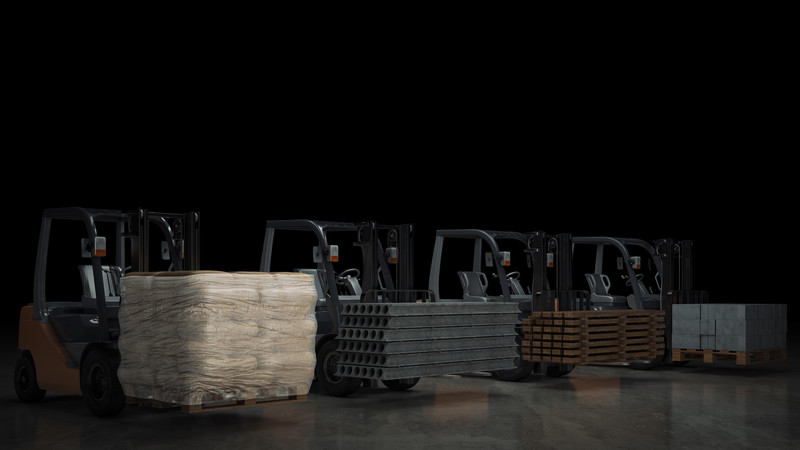
As a Sourcing or Purchasing Manager, understanding what your warehouse’s capabilities are ahead of an engagement will not only save money but will save time and hassle. Warehousing may seem very cut and dry, but it’s not. As a decision-maker for your company, you would be well served to learn and understand the basics of public warehousing capabilities and why they’re important to you.
Material Handling Equipment
In warehouse speak, material-handling equipment generally refers to any piece of equipment used to move or handle your pallets, drums, or freight being stored.
- Forklift – The Forklift is typically the main piece of material handling equipment used in warehousing. Like cars, forklifts require regular maintenance. They are serviced based on usage intervals. According to Bell Forklift, “Propane forklift hours are often listed by running hours, the time the key switch is in the “on” position. Electric lift trucks usually have maintenance intervals are based on hydraulic/drive motor running hours.” As a consumer of warehousing services, ensure that you ask about the age, hours in use, and maintenance and replacement schedule of your warehouse provider’s forklift fleet.
- Drum Grabber – A drum grabber can be a stand-alone piece of equipment or an attachment to a forklift. It’s used to grab and move drums of material. A single drum grabber attachment can move one drum at a time. A dual or quad drum grabber attachment can move two or four drums at a time. If your product is stored in drums, understanding what your warehouse’s capabilities are to move those drums can mean time and money. If the warehouse uses a manual drum dolly, it’s going to take four times as long to load and unload that shipment.
Lifting Capability
Forklifts come in a variety of weight lifting capacities. Some forklifts are rated to lift 2000 pounds, while others are rated to lift 5000 or 10,000 pounds. If your material is heavy, it’s going to be a good idea to understand in advance whether or not your warehouse has equipment rated to move the weight of your product. Learning after the fact when the truck is on the dock is going to cost time, money, and may leave you without a way to store your goods.
Hazmat
While it may seem like common sense, not every warehouse is certified to store hazardous materials. Like any service used to move or store hazardous materials, warehouses must be specially trained and certified to store and handle any hazardous materials. For example, corrosive material may not be stored next to food. Examples of hazardous materials include:
- Chemicals
- Corrosives
- Flammables
- Combustibles
If your company will need to move and store hazardous materials, ensure your warehouse and freight handling companies are Hazmat certified.
Security
Unlike some industries, the warehousing industry doesn’t have regulations around physical security. One warehouse may have exterior fencing with barbed wire and motion-activated lighting, while another may have nothing but the lock on the door. Your appetite for risk regarding the security of your warehouse will likely depend on what type of products you’re storing and shipping. If your manufacturers or clients require a certain level of security, it’s best to find out in advance if your warehouse is suited to meet those standards. It is also prudent to understand in advance what happens in the event of a break-in or theft of your product. If your product is being shipped from overseas and is stolen from the warehouse, you may get an insurance payment, but the replacement product may not arrive for 60-90 days. Customer orders will be delayed and will likely cost more time and money than whatever money is received from an insurance claim.
Software
Warehousing management software makes inventory management at your warehouse much more efficient. Increased efficiency means less time spent on finding and tracking your products when they are ready to ship. Good warehouse management software will be able to do more than just track your products. Ask your warehouse if their software can:
- Provide customer access via a web portal. This is where you’ll be able to log in and see your activity.
- Integrate with your existing ERP system
The more insight and access you have will allow you to better manage the warehousing and shipping components of your supply chain.
Rail Siding
While simple in concept, this is one area that’s often overlooked by clients seeking a public warehousing partner. Will the product be arriving via railroad to the warehouse? If so, is the warehouse located next to the rail line or will trucks need to move product from the rail cars to the warehouse? For more information on rail siding, read Public Warehousing Rail Siding 101.
Hopefully, after reading this article you understand a bit more about warehousing capabilities and what to look for in a public warehousing partner. Don’t be afraid to ask your warehousing professional the tough questions in advance. Learning ahead of time what they can and can’t do may make the difference in keeping or losing a client.
Click below to learn about the Hidden Costs of Warehousing and What it Could be Costing You!